Turn Up the Fuel on a 6.2 - 6.5 GM Diesel Mechanical Injection Pump
Edited and Intro by © Copyright 2004 Chuck Kopelson 12/26/2004
Updated August 1, 2006
Leaking Mechanical Injection Pump:
The army said it often happens and they leave it like that unless it doesn't stop if the engine warms up.
Seals in the pump have the tendency to collapse if it's cold. A stream of fuel in the valley is the result which drains through a hole and drops to the ground.
After the engine warms up the seal swells up and the leak goes away.
I can't live with that so the pump goes to the rebuilder in the morning. $250 for your own checked and sealed and $325 for a rebuilt one. Both include a 6 month warranty.
It takes at least 2 hours to take the old one out.
You have to remove the intake manifold, oil filler, the 3 bolts (13mm) in the hole from the oil filler (don't drop them). Too get to all off them turn the crankshaft with a 24mm socket while someone else checks the hole for the next bolt.
Take the wires and hoses off the pump and your done. The lower injector lines are a pain to get off. You may have to take the lines off the injectors.
Increase Fuel
The reason you would want to increase the fuel supply to an engine is to get more power. All engines need a combination of fuel and air in the right proportion to burn. A diesel engines throttle is controlled by the amount of fuel injected into the cylinder. A diesel does not throttle the air intake like a gas engine. This means that most of the time there is more then enough air in the cylinder during combustion on a correctly setup diesel. If your diesel has more then enough air available at full throttle that means that you could increase the fuel until the correct fuel air ratio is met and gain more power. If you modify the engine to breath better this would increase the available air allowing you to increase the fuel for more power. Typical ways to increase the available air would be installing a low restriction air filter, exhaust system, a turbo / supercharger and modifying the heads.. Obviously you have to do all of this and stay within the design limits of the engine. More power generates more heat and increased stress on the internal components. That's why the turbo diesels have high capacity water pumps, oil spray on the bottom of the pistons and a lower compression ratio.
I asked Tony if he could really feel the difference. Here's what he wrote me.
Let me describe it this way, every Humvee and NA Hummer I have been in to date had to apply full throttle taking off from a stoplight in traffic (and still couldn't keep up with traffic), I can now accelerate the same from a stop with a lot less pedal, and move out pretty quickly if I floor it. The second thing I noticed was hills, I now maintain speed on the ones that used to slow me down, and the ones that I used to maintain speed on I can now increase speed on. It's not as fast as turbo diesel, it is faster than a stock NA. I would say it feels like halfway between a stock NA and a stock TD. Not a tire burning muscle car by any means, but much better IMHO. The stock NA Hummers are very slow and every little bit helps.
Warning: Turning the fuel up on your engine will cause more internal heat that could melt your aluminum pistons. It is important that you be conservative with this adjustment and carefully watch your EGT (exhaust Gas temperature). High EGT can cause piston damage. Buy and install an EGT gauge to monitor temps. I do not have a gauge yet, but I have set my pump conservatively and do not see a lot of black smoke which is unburned fuel. High EGT and black smoke go together. I do not tow or hold the engine at full throttle for more than a minute or two in traffic. If you tow frequently or use maximum power for extended periods high EGT temps will damage / melt pistons. Short EGT spikes are not a problem because they don't keep the pistons hot for long enough time to hurt them. If you ignore my advice and turn the screw up all the way you run the risk of ruining your engine.
I turned up the fuel by taking off the small cover on the drivers side of the injection pump. It is very small, and has 2 screws holding it on. You will need to remove the throttle cable and bracket to see the cover. Once this cover is off, a little bit of fuel will spill into the engine valley. What you are looking for is a small 5/16th Allen screw under this cover that appears through a small access hole. The screw rotates as the engine rotates so you will need to have a large ratchet or breaker bar on the crank pulley nut to rotate the engine while you look for the screw to appear in the access hole. You will need a small flashlight and mirror to see this screw. At first it seemed like there wasn't enough room, I swore I would have to remove the intake manifold. It helps to have a buddy turn the crank while you watch for the screw, but I did it my myself, it just took a lot longer. It does help to remove the throttle cable bracket and detach the throttle cable from the injection pump. You may also have to move the throttle linkage to get to the access cover and fuel screw.
Once the screw is in sight use a good quality 5/16th allen wrench to turn it. To increase fueling, turn the screw clockwise. It helps to turn it in small increments. I turned mine 1/6th of a turn ( imagine from 12 O'clock to 2 O'clock) This gave a good fuel rate to match the increased airflow from a K+N air filter and Kascar (www.real4wd.com) resonator exhaust pipe. I could have possibly gone to 1/4 of a turn clockwise, but I wanted to be conservative. It is important to increase airflow along with the extra fuel or you will just put out a lot of black smoke without any extra power. Once the screw has been turned put it all back together and enjoy.
Here are some instructions found on a ford diesel website, from 85-93, the ford diesels used the same injection pump as the 6.2/6.5 did, the Stanadyne DB2. FYI, the electronic diesels use the Stanadyne DS4, and the fuel rate is calibrated by the computer, not a screw.
From the Ford diesel site:
You will need a small mirror (one from your wife's purse works very good). 1/4 inch wrench. a 5/32 allen wrench, A good portable work light. A socket that will fit the bolt that holds the harmonic damper on (mine was 15/16), a short extension, and a breaker bar.</
1. Make sure your engine is cold before you begin.
2. Unplug the two top wires going into the top of your injection pump.
3. Take the ground wires loose from both batteries.
4. Use the appropriate socket, extension, and breaker bar and turn your crankshaft VERY SLOWLY CLOCKWISE.
5. Lean over the front of the truck. In this position you will see a little plate on the left side of the pump way down low. Remove the cover.
6. Put the cover , rubber gasket, and two screws away in a clean place. Dirt and injection pumps don't mix. Be careful not to damage the rubber gasket as you will have to reuse it.
7. After you have removed the cover, lay the small mirror to the left of the pump. angle it so you can see into the pump. Towards the rear of the pump where the cover was removed, you will see that the hole in the pump case tapers to a point. Looking in this area you can see a hole deep in there. Behind this hole you should see the allen screw appear as you turn the crank. Look close because it is hard to see. If you don't see it, you will have to turn the crank some more.
8. When you find the screw, insert the allen wrench into it.
9. If you are just increasing fuel without any other modifications, I would not turn the wrench over about 1/8th. WIth intake and exhaust improvements 1/6th, with a turbo 1/4th. You can always turn it up a little more at a later date. To increase the fuel supply, turn the screw clockwise. It is a self locking screw so it is not easy to turn. Use a good quality allen wrench. You may need a wrench on the allen wrench for leverage.
10. Replace the cover being careful about the gasket and dirt. Do not over tighten the screws, remember they are very small and strip out easily.
11. Make sure you didn't leave the socket/ extension bar hanging on the harmonic balancer.
12. Reconnect the two wires to the fuel injection pump.
13. Reconnect the battery cables
The truck may be hard to start due to the drained fuel pump (mine was easy to start). Do not crank the starter more then 30 seconds at a time with a four minute cooling interval.
REMEMBER: Turn your engine very slowly when you are trying to align the set screw using a breaker bar NOT the starter. Changing the fuel setting works best in conjunction with better airflow from intake/ exhaust mods. You will not realize much gain without increasing the exhaust size and making intake improvements.
There are actually 2 ways to reach this screw, the side as I did, or the top of the injection pump. I chose not to remove the top because the governor assembly is there and must be removed and reinstalled to get to the screw. I was afraid of this because I have heard that if the governor is reinstalled wrong, the engine could run away ( RPM's keep going up until it blows). So I chose the harder to get to, but safer access through the side cover.
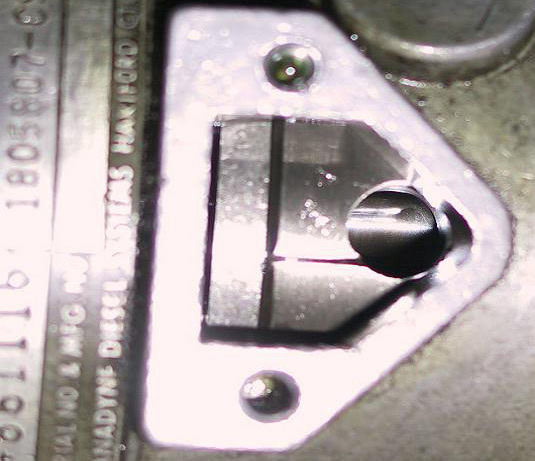
This is the side cover access hole with the screw out of sight, the crank needs to be rotated to see the screw through the hole.

This is the fuel screw, aligned with the access hole, adjust it clockwise to increase fuel. A small adjustment makes for a lot of fuel, think of it like a clock, 1/4 turn would be from 12 to 3, so you want to go less than that. The Banks turbo kits for GM diesels recommends 1/4 turn, but for an NA engine, you want less fuel, so 1/6th is about all you can do safely.
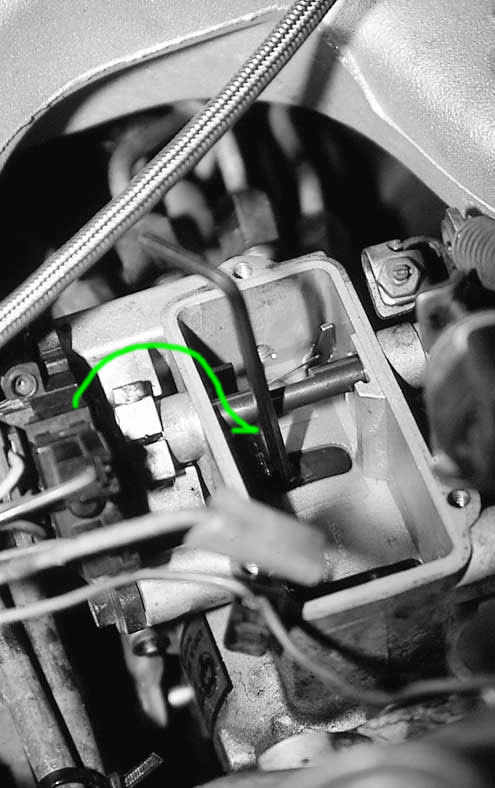
Same rotation of the same screw, just another way to get to that screw. In this picture, the allen wrench is in the fuel screw.
Top View of injection pump with the top cover and governor assembly removed. Suck the fuel out with a turkey baster.
How to change out a mechanical injection pump.
1) remove the inner engine cover and remove the intake manifold.
2) remove the hard fuel lines
3) remove the oil fill tune on the engine.
4) take and mark the injection pump housing to the timing cover. (this will help later)
5) remove the 3 bolts on the inside of the hole that the oil fill tube was. you will need to turn the engine over until each bolt lines up to the hole where the oil fill tube was. turn the engine over by hand only or you could damage the cam drive gear woodruff key and you don't want to go there.
6) remove the 3 nuts holding the injection pump to the timing cover.(these are facing the windshield where the injection pump meets the back side of the timing cover)
7) remove the injection pump. (oh yea and don't forget to remove the fuel inlet line) that's the one in the middle of the rear of the injection pump.
8) . transfer all parts that are not on you new pump.
9) reinstall the pump in reverse order. try to line up the timing mark that you made on the old pump to the timing cover.
10) you can start the engine without the intake manifold to make sure there are no fuel line leaks.