Install a High Output Alternator in Your H1
Battery Article
Fast Idle Switch Article
© Copyright 2000 - 2007 Chuck Kopelson 09/18/2007
Updated March 9, 2008
The reason we wrote this article was to head you off from possibly wasting your money on HO alternators. Our design criteria was more amps at idle so accessories don't drain the battery when standing still. We found that the 125 amp stock alternator was fine at higher RPM where you got full output. Below is the story of how we came to believe this. The bottom line is that in order for the HO alternators to output more power at idle it has to spin at a higher RPM. In order for this to happen it needs a smaller pulley. You can't use a smaller pulley in the existing hummer setup. The belt won't stay on because the tensioner goes over center.. The best solution is to use a stock alternator and hook up a high idle switch.
There are HO alternators that give you more power in the higher RPM range than the stock unit that work well.
Jim Bennett replaced his CS-144 125 Amp alternator with a CS-144 200 Amp unit because he had trouble keeping the batteries charged. The alternator only output 8-12 volts. The new alternator is supplying between 13 to 14.9 volts at idle and at 1800 RPM. Batteries are relatively new and checked out OK .
There were a couple of issues installing the new alternator. The new alternator is deeper due to the external dual rectifiers and didn't fit the same and an electrical problem. it turned out that they were related.
There was an intermittent battery light coming on about every 10-15 minutes. It stayed on only about 1-2 seconds and went out after another 10-15 minutes. There wasn't any voltage variation when the light came on. I thought the light is in series with the Alternator field and if it lit would indicate the battery is discharging.
An intermittent short from the alternator output post to the valve cover was discovered. The new alternator's orientation to the stator case was 90 degrees different from the stock alternator. It was noted during the install and a piece of heat shrink tubing was used to insulate the post. The engine must have heated up the sleeving which shrunk, became thinner wore a micro sized hole causing the short.
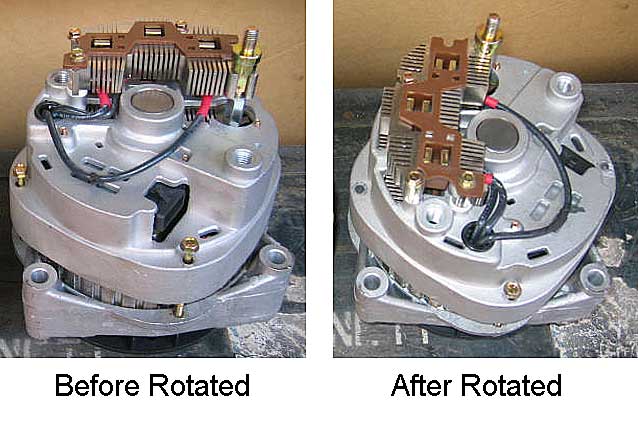
You rotate the case by simply unscrewing the bolts and turning the case. Don't pull the case apart. There was still insufficient clearance between the upper edge of the external dual rectifier bridge heat sink. That meant the bracket that secures the fuel feed line to the right side injectors had to be removed.
With that, the alternator slid into the two foot mounting pads. Also note that the stock mounting bracket to the rear side of the alternator must be removed because there is no clearance for the diode bridge.
Removing the truck's rear mounting bracket can possibly cause sneak current flow from the rear stator windings to ground through the rear assembly bearings theoretically damaging the bearings from overheating. The bracket provided the return path to ground for the alternator's rear stator winding.
To solve this I attached an 10 inch piece of large braided shield to the alternator rear housing and connected it to the engine block where the front housing bolt attached to the engine.
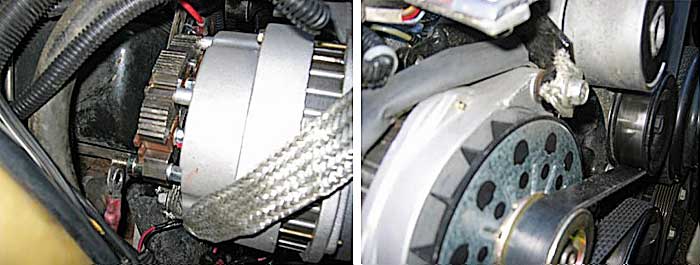
I noted that there is only a 65 millivolt (.0065) volt difference between the alternator output post and the battery positive post. That means there is insignificant drop to the battery and this unit should work out just fine.
Experimental Notes:
The Hummer has a electric window heaters in the windshield to melt ice and snow in the winter. This is a great feature but the stock alternator a CS 144 (CS is 'charging system and 144 is the OD of the stator in mm) is a 124 amp unit that won't always keep up when the engine is at idle (650 rpm) when a few other accessories like the defroster, heater and headlights are on. I tested this and noticed that the voltage dropped to 12.1 indicating the batteries are being discharged. This isn't necessarily a bad thing. The batteries are designed to supply power to the truck when the alternator doesn't have enough output. In fact the alternator is designed to keep the batteries charged. Once the truck comes off idle or the accessories are turned off the battery will recharge.
I received the Fluke DC current probe and did some testing tonight. I was very surprised at what I found.
First the engine requires 11 amps just to run.
Second the running lights pull 12 amps and the headlights pull another 12 amps for a total of 24. I do not understand why the running lights pull so much. I measured one tail light bulb on a lab power supply an it pulls about 1/2 amp. So the lights on the 4 corners would pull about 2 amps. The hood is up so the hood light is probably another 2 amps. That leaves 8 amps for the 14 maker lights which seems a bit high. I think changing to led lights could save about 8 amps.
My fog lamps pull 9amp.
The main heater blower will pull 17 amps on high. The wire direct to the alternator is only used when the blower is on high. Otherwise the power comes from the cabin.
The rear blower will pull 12 amps on high.
Both fans on low pull 8 amps
The AC clutch pulls 3 amps.
The alternator I am using now is making about 80-83 amps at idle with the battery voltage at 12.8 to 12.9. If I hit fast idle, I can get the current ext bus current up to 132 by switching on the light bar with the battery at 14.0. I forgot whether the front blower was high or not. IF it was, the alterntor would actually be putting out another 17 amps.
A problem occurs if you use your accessories for a prolonged period and drain the battery low enough so the truck dies and won't start. This could happen if you are using an electric winch, an array of powerful lights, snow plow or a high power sound system. Another factor is that a discharged battery will freeze up faster than a fully charged battery. Running your battery down in the winter is not a good thing.
The biggest market for high output alternators is mainly for the 'big rigs' where over the road drivers are living in their extended cabs and sleeping overnight. Their trucks might sit and idle for 7 or 8 hours at a time running accessories like air conditioning, heaters, refrigerators, TV's, CB's and lights. If the accessory load exceeds the alternator output the batteries can easily run down.
How to Estimate Your load :
This is a great pdf Document from Delco Remy
Here's the quick and dirty on how I did it.
- Front window heaters 37amps
- Head lights 15 amps (70 watt Hella H4s)
- Defrosters & heaters 10 amps (AC compressor clutch and 2 blower motors)
- Light bar with 6 Hella dual 55 watt bulb worklights. (50 amps)
This adds up to about 112 amps which is over the expected output of a stock alternator at idle. It does not include things like brake lights, power for the engine computer,
electric wipers, turn signals, trailer lights and accessories.

The alternator I bought for a model year 2000 truck is the 200 amp Excel 8060-4HO which was 160.00 plus a 50.00 core charge and 10.00 shipping (9/2007). This model is good for model years 1996 through 2001. I bought it from Excel HO Alternators. According to Excel "These units were engineered by us in response to a persistent problem encountered by police,taxi, and other heavy duty applications where high load combined with long periods of idling was causing a discharge condition."
The new alternator has a smaller pulley; 1.875 vs 2.150 so you will need a 100.5" serpintine belt. I bought an Autozone Duralast 1005K6 belt which is one inch shorter than a stock belt. (101.5 vs 100.5). My initial concern was that the new belt might be too short. I could barely get it on and the tensioner was about 2/3 compressed. After running it for a while the belt stretched out and the tensioner has moved to the half way point. I exchanged the belt for a Goodyear 100.5" Gaterback (4061005 - 6KP2555) which cost me 31.00. I tried to put a 100 inch belt on but there was no way. I put the 100.5 on and it's doing the same thing that the Autozone belt did.
This has now become a big problem. The belts have stretched some. Another issue is that the smaller pulley on the alternator changes the geometry / belt angle to the tensioner so that the last 1/4 " of travel is useless. At a certain point the tensioner fails to tighten the belt and just moves to the end of it's travel. The tensioner has now gone overcenter and won't tighten the belt at all.
Another owner installed a high output alternator from alternatorparts.com and used the larger 2.5" pulley. He thinks that all alternators are not designed for continous full output. Therefore the HO alternator might be working in the continous duty range all the time. Running it at a lower rpm means it will turn slower and the bearing will last longer. If he needs more power while idling he installed a high idle switch.
The crankshaft pulley at about 7.75 inches in diameter and the new alternator pulley is 1.875. This is about a 4.1 ratio. If you do the math it comes out to (650 * 7.75) / 1.875 = 2,686 rpm. The stock alternator turns at 2,343 rpm at idle. Supposedly the HO alternator can make 190A at that speed. Personally I think something would smoke if I tried that.
The HO alternator uses a smaller pulley for two reasons. More RPMs means more power and just as importantl more airflow. This alternator will get hot when generating 100+ amps at idle. Heat is the enemy of your alternator.
I did a preliminary test at idle. The new alternator seems to handle everything I can switch on including the light bar. I estimate the load at over 100 amps. This curve indicates this alternator should make almost full output; 180 amps at idle which is 2686 rpm at the alternator.
I'm thinking of upgrading some of the wiring. I am getting about 1/3 of a volt drop between the battery and the external power bus. I might need to increase the wire size. I am also seeing about .1 volt drop on the ground. Even so, I can switch on the front window heaters and my light bar and maintain 13V on the panel meter.
The instructions with the HO alternator tell you to put an extra wire with a #12 fusible link in parallel with the existing battery cable. I put a #4 wire with two #14 fusible links in parallel with existing battery cable. I am not sure if this is desirable, safe or unsafe. I am beginning to think the correct thing to do is to replace the stock battery cable with a #4 cable with two #12 fusible links. I also think that I need to upgrade the wiring between the alternator and external bus because I am seeing a significant voltage drop there.
I think this is still a work in progress.
While researching this article I came across this site which has a lot of good articles on electrical systems.
The direction sheet that came with the alternator says the following:
- In order to ensure proper vehicle safety the wiring to and from the alternator will need to be upgraded.
- We recommend running a parallel circuit using a 12 gauge fusible link from the output post of the alternator to a positive battery source. Be sure the positive battery source has no other circuits between it and the battery.
- This circuit is in addition to the vehicles original wiring.
- It is best to solder all connections in this parallel circuit so there is no chance of arcing at the connection ends.
- Also make certain that the negative path from the alternator is large enough to handle the extra output. This will usually be OK since most vehicles use the negative battery cable as the ground path to the engine block.
Alternator connections.
I = Ignition wire
Output wire to the Battery positive
The SFLP connector
- S is connected externally to a voltage such as battery (heavy gauge wire) to sense the voltage to be controlled.
- F is connected internally to field positive and may be used as a fault indicator.
- L is connected to a charge indicator bulb (idiot light) that lights if a defect is detected.
- P is connected to the stator and and may be connected externally to a tachometer or other device.
Delco Remy Service Manual
R = relay terminal has pulse frequency that varies with rpm for use by a tach.
Stock Alternator
The stock alternator senses the voltage at the alternator. If you look at the Hummer wiring diagram you will notice they use the alternator as the junction block (not all years) , so it makes sense to sense the voltage right there. The stock alternator requires an external voltage to energize it and there is a small connector on the alternator. This is called a 2 wire alternator. Alternatorparts.com has some good info on this.
http://www.alternatorparts.com/what_is_a_self_exciting_alternator.htm
The Hummer stock alternator is a standard GM CS144 alternator which is considered to be one of the best. You can find lots of info on CS144 alternator
This might be a matter of semantics. In 2000 the alternator hooks to the battery and feeds the external power bus. The starter hooks to the battery and the glow plugs hook to the starter.
Battery – alternator – ext power bus – internal power bus
|
|--- starter – glow plugs
In this configuration, sensing the voltage at the ext power bus would over charge the battery because the alternator would increase the voltage to compensate for the drop in the wiring but the battery would see the entire voltage.
The best configuration would be to connect everything to the ext power bus in a star configuration but this would require more wire and therefore cost more. An easier solution is to increase the wire size between the alternator and ext power buss so there is less voltage drop.
There is one wire in the plug going to the alternator. I believe this wire is to activate the field when the ign is on.
I looked at the tensioner tonight and found it all the way to the end.
Apparently the belt has stretched quite a bit. The smaller pulley on the alternator changes the geometery so that the last 1/4 of the tensioner travel is useless. At a certain point the tensioner fails to tighten the belt anymore and just moves to the end of the travel. To make matters worse once the tensioner has moved past a this point it an increase in belt tension will not rotate the tensioner.
I am contemplating this problem. I can get a shorter belt but I don't know if a 100 will even go on but it would probably be fine after the initial stretch. I wonder if the autozone belt has stretched more than a name brand belt. A larger pulley (but smaller than stock) might is another possible solution.
I drove the truck about 12-15 miles today and new gates100.5 inch belt bottomed out just like the autozone belt. Total time on the belt was about 30 miles of maybe an hour of run time.
I installed the gates 100.0 belt by routing it differently. I put it on the opposide side of the vacuum pump pulley and it fits well. I ran it for a while in the garage with heavy load on the light bar and AC and I could see it stretch after a short time. I took it for a drive and the tensioner was bottomed out when I got back but the belt was still too short to route correctly. I will let it set and run it some more to see what happens. I am wondering if I can reposition the tensioner so the arm does not swing as low so I can use an even shorter belt. I need to get the correct torx to remove it and see.
do you think I should change the alternator pulley to stock and call it quits?
I realized last night the putting the belt on the back side of the vacuum pump causes it to run backwards. Not sure if that would damage it.
I will pull the tensioner tonight and then just go back to the stock pulley.
I called excel and told them I had a technical problem and they let me talk to Paul. I explained the situation and Paul advised me to install the old pulley on the new alternator. I asked if we should try a size in between the new and old and he said that is just splitting hairs. The old pulley will give a 3.6 instead of 4.1. Looks like alternator speed will change from 2600 to 2300 at idle which should still be ok.
I put the original pulley on the HO alternator. This is a simple job with an impact wrench but nearly impossible without one. Hold the fan with your hand and the impact will spin the nut right off. If the pulley won't come off after removing the nut, put a hex key in the end of the alternator shaft, hold the shaft and turn the pulley by hand to remove it.
The old pulley has a spacer behind it which must be transfered to the new alternator. I also opted to use the original nut since it was thicker than the new one. The new alternator has a lock washer and the stock alternator has a flat washer behind the nut. I decided to use all the original hardware.
The belt tensioner worked perfectly with the original pulley and belt. My initial impression was that the HO alternator can produce the same power as the stock alternator at idle with the original pulley. After some driving I am having doubts that it produces as much as the stock alternator. When I step on the brake the voltage immediately drops from 14 to 13 and sometimes comes back up to 14 after stopping. With the headlights on (and nothing else) the voltage might sag even lower. It seems like the HO alternator is right on the edge at idle with the stock pulley.
I engaged fast idle (1070 RPM) and switched on the lightbar, headlights, foglights and window heaters. The interior voltmeter stayed above 13V indicating the alternator is indeed capable of high output.
Since I cannot make the belt tensioner work with the small alternator pulley and the HO alternator does not produce any more (and maybe less) power than the stock alternator with the stock pulley system, I consider this project a failure at this time.
It also tells me that the curve they publish is total BS. The alternator is spinning at 2300 RPM and should be producing lots of power but it seems to be right on the edge of turning on. Since the alternator loads up well at fast idle, I don't think the belt is slipping either.
If I could make the belt system work with a smaller pulley, any alternator would do the job.
I measured the voltage with a good meter. I get 12.75 at idle and 14 if I speed it up. Definately worse than a stock alternator.
I am trying to calculate the belt change based on reducing the belt size. It seems like there are two factors. One is reducing the pulley size effectively moves the pulley closer. The amount closer is 2 times the radius because you are shortening both sides of the belt. The second factor is the circumference of the pulley is smaller. The belt wraps close to 1/2 of the pulley so the change is 1/2 the circumferance of the pulley.
Original pulley circumference = 2.15 * 3.14 = 6.75 new pulley circumference = 1.875 * 3.14 = 5.89 circumference delta = 0.86 use 1/2 this amout because the belt wraps 180 degrees.
radius delta = 2.15/2 - 1.875/2 = 0.1375
belt change = 1/2 circumferance delta + 2 * radius delta = .43 + .275 = .7
This correspondes well with the fact that a 1 inch shorter belt initially fit well.
The next step is to determine if increasing the idler pulley size on the tensioner will compensate for the smaller alternator pulley.
The idler pulley is 3 inchs but only wraps about 1/4 the pulley with the standard belt configuration so any increase in idler pulley circumferance is divided by 4. It also does not appear that the change in pulley diameter has much affect because the tensioner will move to a new position.
So change the diameter from 3 to 3.5 will change the circumferance from
9.42 -> 11 but 1/4 of this is .4 inchs. This does not appear to be enough to compensate but it might make the geometry of the tensioner work better.
Do you think this is work experimenting with or will it be another wild goose chase?
I called excel auto again. They told me that even a 100 RPM alternator speed change can be a huge difference at idle. They also said there is some variance unit to unit and they he will check several units to see if he can find one that works better at low RPM.
According to alternatorparts.com, you cannot get more power at idle by installing a HO alternator. It seems that a HO alternator trades low speed performance for HO which is why they need a smaller pulley. Chris at excel auto made similar comments.
I also asked chris about using a different tensioner or larger pulley on the tensioner. He said that a 3 inch pulley is already a pretty big pulley for the tensioner. I looked at the tensioner swing and it is fairly close to the fan pulley but there is some extra room. My logic here is that it might only take a 1/8 inch increase in idler pulley radius to compensate for a 1/8 decrease in alternator pulley radius.
I would hope to find idler pulleys in various sizes. A quick trip to NAPA would find out.
A google on “idler pulley serpentine” turned up a 3 5/16 and 3 ¼ and 3 ½ back side idler pulleys that might work. The 3.5 might hit something though.
I was thinking of wrapping the stock idler pulley with tape to increase the diameter for a static test before buying or making a pulley. I might need to change the arc so that the tensioner cannot swing as far down.
Maybe chris will find me an alternator that will work at low RPM but this is still not a good solution.
Chris called back and told me that he hand selected components to build an alternator with a 300 RPM lower power curve that should work fine with stock pulleys. The only draw back is that it will reduce the max output current from 230 to 185.
He says that if this does not meet my application, they can machine parts from a bigger alternator to fit inside the CS144 case. I sure wish I had known about this option in the first place.
He is really wishy washy on idle output. In fact nearly everyone is vague on idle output. He claims that even 100 RPM at the alternator can make a huge difference. He quoted some numbers but I don’t remember exactly. I THINK it was the alternator turns on at 1500 with about 4 amps. It can make 50 amps at another number like 1800 or 2000. So the bottom line is I don’t know the idle output. All I can do is install the new alternator and see if it pulls the load. If I don’t like, send it back and try the next option. Based on my calculated alternator RPM, the standard HO alternator should be making lots of power but it doesn’t seem to meet reality.
The HO with stock pulley is definitely putting out less that the stock alternator. It will only run one accessory at idle and keep the voltage above 13. I can even see the voltage change by switching the fan speed from low to high.
Actually I think the better option is to find out what bigger alternator they can cram into the CS144 case. This alternator is right on the edge and seemed to work ok tonight. I suspect that his custom built one will work ok, but it still makes me want to learn more about the alternative.
The HO with stock pulley is definitely putting out less that the stock alternator. It will only run one accessory at idle and keep the voltage above 13. I can even see the voltage change by switching the fan speed from low to high.
Actually I think the better option is to find out what bigger alternator they can cram into the CS144 case. This alternator is right on the edge and seemed to work ok tonight. I suspect that his custom built one will work ok, but it still makes me want to learn more about the alternative.